

“Also, using tooling and the adequate volume drilling fluid will help keep drills working efficiently.”īoth major HDD manufacturers continue to add technology that can help reduce costs, including dual rod machines, integrated electronics, and of course, telematics. “As with any piece of equipment, making sure operators are properly trained and following the manufacturer’s recommended service intervals is an effective way to help control operating costs,” Michael says.

Vermeer’s Michael says training operators and crews is important to the cost-management mix. For example, Ditch Witch drills are prepackaged with intuitively located service points, easy-to-use manuals, and quick proper tooling guidelines, which makes HDD preventative care and maintenance straightforward.” Like Ditch Witch design machines with contractor simplicity in mind. “To make this process seamless, manufacturers “This will not only keep machines functioning at high levels, but also prevent costly downtime,” Davis continues.
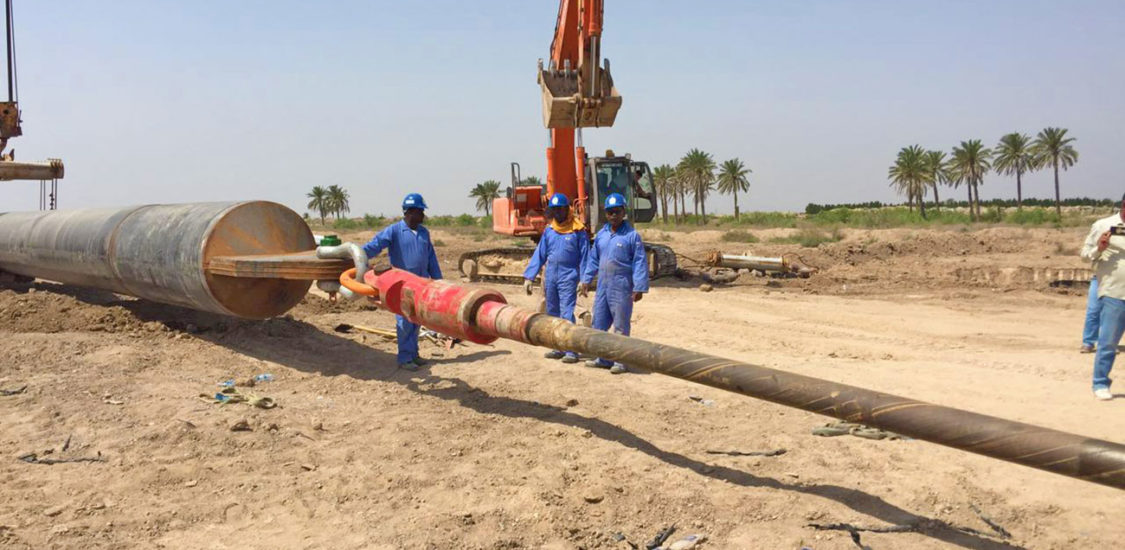
“Following best practices and conducting routine maintenance are two important factors that will help keep operating costs down over the long run,” Davis says. OEMs have incorporated features to make that easier to do, particularly in the maintenance arena. Once in the fleet, the challenge for HDD owners and operators is to keep operating costs down. Total cost of ownership for directional drills “Where are your crews working, and what are the ground conditions like?”įor transportability, Michael recommends asking what else is being sent to the job with the crew, and what size trucks and trailers are being used to move it all there.įinally, on fleet preference, answer how many crews will be running and whether or not there is a desire to standardize fleets or expand their capability range. “When comparing the work your crews spend the bulk of their time on, what are the bore profile averages?” Michael says. He recommends managers review four factors to narrow their HDD search: bore specifications, job site conditions, transportability, and fleet preference. “The model that worked yesterday may not be the right one for the next project,” Michael says. Tod Michael, cutting edge business unit manager for Vermeer, says that choosing the right size directional drill can be a challenge because contractors will often have to manage multiple installations for multiple clients in multiple locations-all with varying ground conditions. “By understanding the relevant applications and ground conditions, customers can clearly communicate their rig expectations to dealership sales reps.” “Before investing in a new drill, customers should first identify required capabilities and needs on future job sites,” says Jeff Davis, HDD product manager for Ditch Witch. One of the first things managers should consider is the nature of the work ahead. Horizontal directional drills are a significant investment, and as with virtually all equipment that engages the ground, sound choices and proper maintenance should produce years of service.
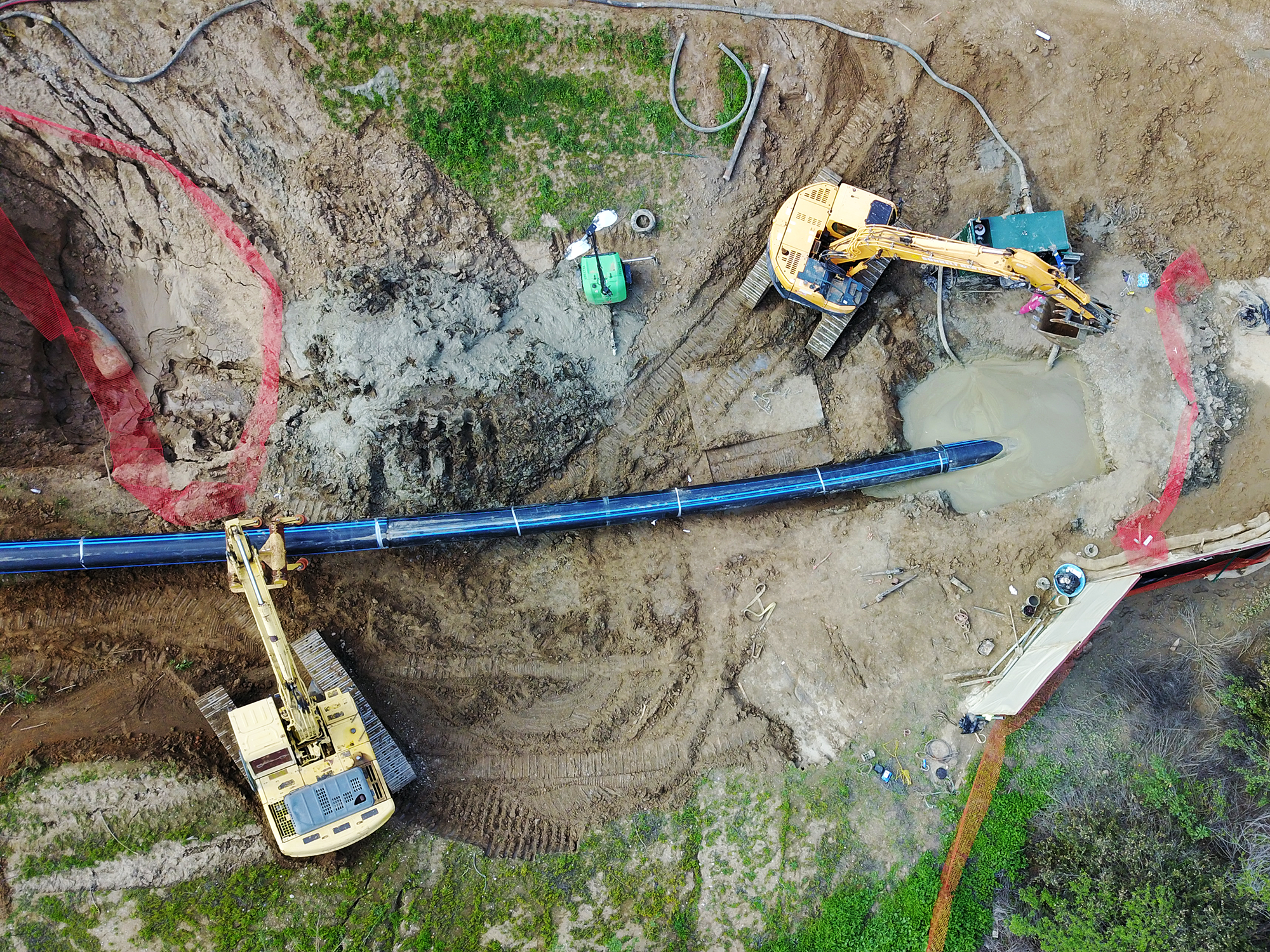
Horizontal directional drill (HDD) giants Ditch Witch and Vermeer both report a strong market for directional drills and continue to invest in technology for their customer bases, including dual rod technology, commonality of electronics and controls, and telematics.
